Leach & Co. is a privately owned waste management and contracting company. It operates Wellington’s Southern Landfill for Wellington City Council.
The company’s biggest energy source and emissions factor is diesel. To align with the council’s sustainability goals, reducing diesel use from their off-road equipment was a clear target.
In 2023, the company bought its first electric off-road vehicle – a 20-tonne loader. A year on, the team couldn’t be happier with its performance. With the introduction of the new electric loader, the business has cut around 25,000 litres of diesel per year from its operations.
This case study covers how they did it, how their costs stack up, and what they’ve learned along the way.
Project Summary
Company: Leach & Co
Industry: Waste management
Site region: Wellington
EECA co-funding: $104,000 from the Low Emission Transport Fund
Year of funding: 2023
Loader purchase price: $429,295
With help from EECA’s Low Emission Transport Fund, Leach & Co. imported the first ever electric wheel loader to be used in a New Zealand landfill, the third of its kind in the country.
The XCMG 20-tonne, battery-electric, front end wheel loader XC968EV replaced its 15-tonne diesel wheel loader. The electric loader has a bucket capacity of 3.5m3 and a rated load of 6,000kg.
Savings achieved
- 25,000
litres of diesel per year
- 40 %
savings on fuel cost compared to smaller 15-tonne diesel loader
- 7 %
reduction in total carbon footprint
There is a large amount of pride amongst the team that the company is investing in the future. We are making a difference.
Exceeding performance expectations
More power
Leach & Co. found that the new XC968EV exceeded its performance expectations and is significantly more powerful, faster and more responsive than their old diesel equivalent.
CEO Eric Souchon said that due to the new loader’s high responsiveness and speed the company ended up reducing its performance settings to help the drivers adjust to operating it.
Improved driver comfort
Leach & Co.’s drivers were impressed by the reduction in noise and vibrations from the operation of the vehicle compared to their old diesel model.
This comfort, paired with the greater responsiveness, means that the drivers are more productive during their shifts, and less fatigued at the end of the day.
Upgrades and maintenance
Given the significantly quieter operation of the electric loader, the company added reversing alerts and additional cameras for safety.
They have also changed the tyres to solid rubber to reduce the high risk of punctures in a landfill environment, and have upgraded the air-conditioning filtration system to better filter out landfill contaminants.
When considering an electric loader, Leach & Co. initially had concern around availability of skilled workers to service electric off-road equipment in the area, but had no issue finding accredited suppliers to smooth out some initial teething issues.
Maintenance costs have also proved to be cheaper – servicing takes just one and half hours compared to half a day for the previous diesel machine.
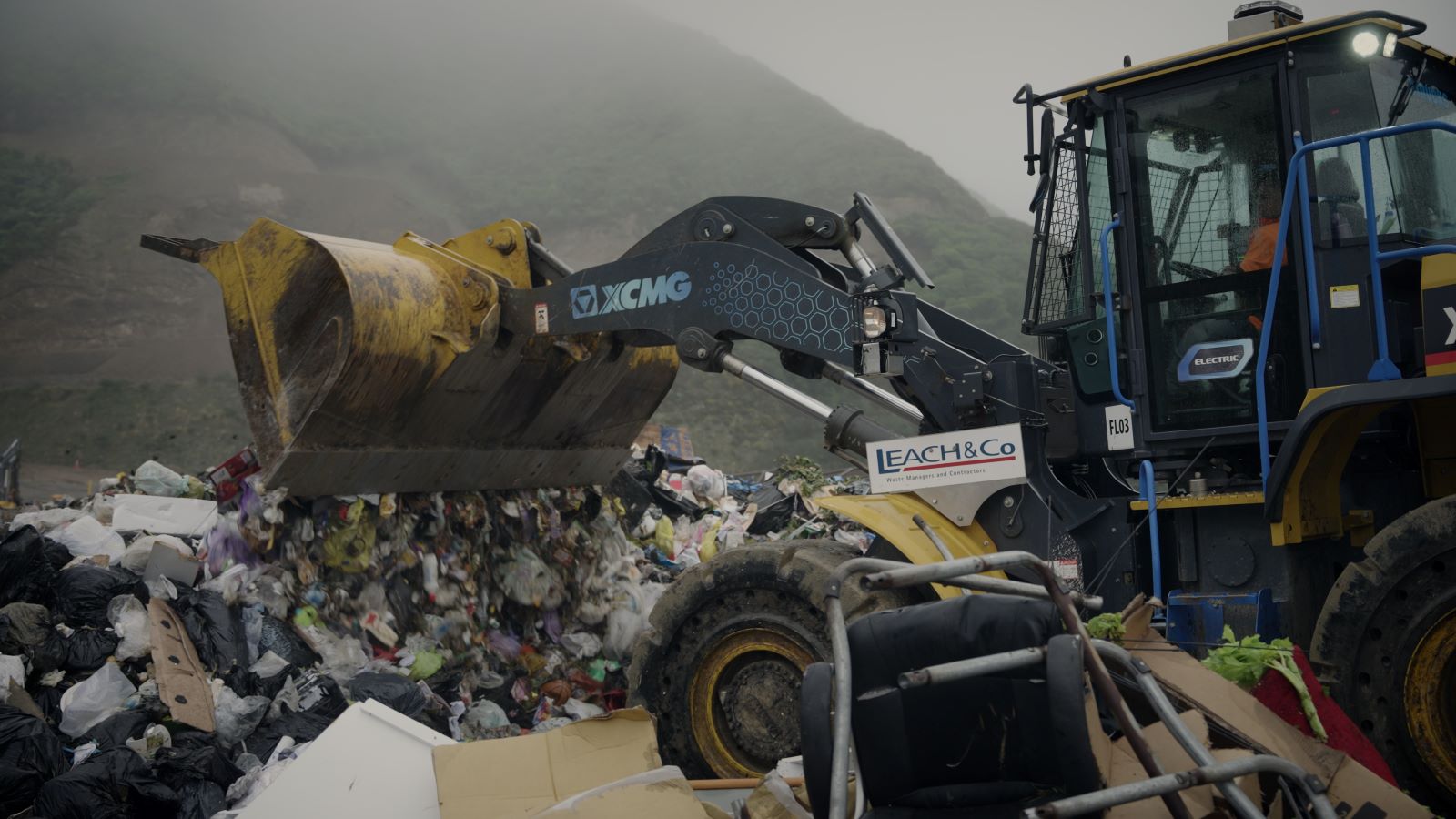
When you take the risk to move to new technology, you want to know it’s going to perform. Fair to say, it’s delivered better than expected.
Lessons on charging
Understand your electricity supply before investing
With a depot just 1km away from the main landfill site, setting up access to a charger and power supply was relatively easy for Leach & Co. For more remote sites, access to adequate electricity infrastructure can pose a significant challenge.
Nevertheless, Leach & Co. had to carefully consider the site’s electricity capacity to ensure sufficient supply was available. They opted to install a 90kW charger, which is the most the site could take without extra electricity supply capacity.
Leach & Co. recommends talking to your electricity supplier early in the process and allowing sufficient time for charger installation in your project plan.
Consider charging time and impact on operation
Leach & Co. had to consider the practicalities around charging times to ensure maximum productivity. The 90kW charger can fully charge the loader in 4 hours, to last a full 8-hour shift. The charger is fast enough to give a substantial top-up charge during drivers’ breaks if needed.
The charger has two charge points, and sufficient capacity to fully charge two machines overnight, which gives Leach & Co. scope to expand their electric fleet.
Over time, the team has developed techniques to use the loader more efficiently. Their policy is to run the battery down to a minimum of 30% before recharging – which helps to prolong the battery life.
Understanding the electricity capacity you have available on site is critical to the whole process.
A comparison of costs: electric vs diesel loader
The XC968EV costs around 1.75 times the price of the XMCG’s diesel equivalent.
As an early adopter of the technology, Leach & Co. was able to offset the higher upfront cost with the help of co-funding from EECA’s Low Emissions Transport Fund.
Going electric has led to significant operational cost savings for the company, which are helping to offset the remainder of the higher purchase cost.
- Leach & Co. is saving around 40% on fuel costs – this is significant as the XC968EV is a much larger machine compared to the diesel loader it replaced (15 tonnes vs 20 tonnes)
- Without the need to replace engine oil and filters, or service a combustion engine, maintenance costs have reduced. Servicing takes just one and half hours compared to half a day for the previous diesel machine.
- Long term, Leach & Co. are assuming the vehicle has an operational lifespan of 10,000 hours (around 5 years for Leach & Co.) before needing a battery replacement. In comparison, the diesel equivalent would require a significant full engine rebuild around that time. Note, this is much shorter than the manufacturer rated 16,000 hours of operation for the electric machine.
How could the costs stack up for your business?
Recent modelling from MartinJenkins and EECA suggests that the total cost of ownership (TCO) can work out cheaper for electric loaders, compared to diesel.
This modelling examines the TCO for the electric XMCG XC968EV 20-tonne loader (like that used by Leach & Co.), and the XC968 20-tonne diesel equivalent.
The calculation includes the cost of the vehicle, a charger, charger installation, fuel and maintenance. With all these factors considered, the electric loader offers a 5% lower TCO, when fully utilised to the manufacturer rated 16,000 hours of operation. These savings are due to the significantly cheaper fuel costs for the electric loader (around 73% less than diesel), and 11% lower maintenance costs.
Further TCO savings can be achieved if the operator has a compatible charger already installed for other equipment, and runs multiple electric vehicles, as the upfront charger installation cost is spread across more vehicles.
We’re looking out towards the future of the brand. We’re very pleased with where we’ve got to. This is the start of a journey, and we’ve got an end game to get to.
Building on success
Leach & Co. is considering further electrification options. Following the results of the XC968EV, Leach & Co. is now looking to get a second electric machine (a 10-tonne, battery-electric loader) at the end of this year.
With the charger already installed with capacity to charge two machines, no additional capital is required to charge the new machine, helping to make the total cost of ownership more favourable for future electrification of the company’s fleet.
Explore support opportunities
We can help your business become more productive with less energy, and support your switch to renewable energy sources.
Read next
-
Electric off-road machines
Businesses around the country are adopting electric off-road machines – and operators are impressed.
- Electric vehicles
- Decarbonisation
- Case study
-
Decarbonising off-road heavy vehicles in New Zealand
A view of the market for heavy duty, electric machines – now and into the future.
- Electric vehicles
- Market research
- Decarbonisation
-
Electric loader delivers energy cost saving
Fulton Hogan’s electric loader reduces fuel costs up to 79%
- Electric vehicles
- Decarbonisation
- Case study