Electric frost fans can save emissions and costs
Frost fans are vital for many growers around New Zealand for the resilience of their crops. These fans are particularly important in regions that experience colder weather conditions that can damage fruit buds and ruin entire crops.
Currently, a majority of frost fans in New Zealand are fossil fuelled. Transitioning frost fans to electric provides growers a significant opportunity to reduce emissions, protect their crops, and lower operating costs.
The role of frost fans
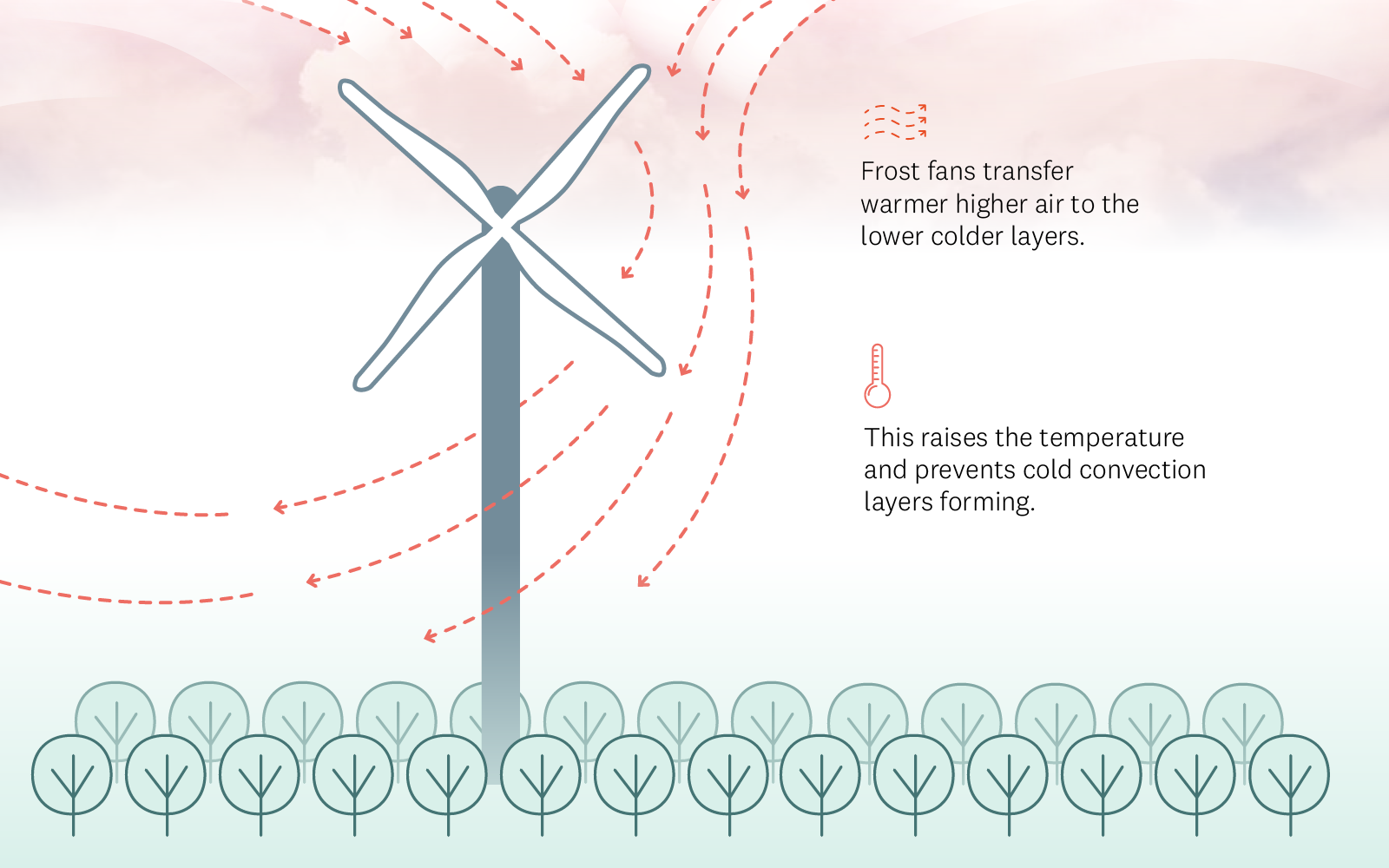
Electrifying the fight against frost
Traditional frost fans are usually diesel fuelled and are the most common type of fan within the New Zealand horticulture and viticulture sectors. They can be expensive to run as well as high emitters, consuming anywhere between 20-40 litres of diesel per hour. Helicopters can also be used to fight frost, but emit higher levels of CO2 than diesel frost fans.
In comparison, electric frost fans are powered by electricity from the grid or from on-site renewable generation, such as solar power. They do not require diesel, making them more environmentally friendly. Due to having fewer moving parts than their diesel equivalent, they also tend to have lower maintenance costs.
Forest Lodge Orchard and the electrification of its frost fighting fans
Spanning over six hectares in Mt. Pisa, Central Otago, Forest Lodge Orchard has been on a journey to become the world’s first fully electric, zero-emission orchard. This has taken four years to accomplish and is saving over $40,000 a year in energy costs for the farm and household.
As part of this journey, Forest Lodge has improved both the efficiencies and carbon footprint of its site, including:
- replacing a diesel irrigation pump with an 18.5kW electric pump
- installing electric heat pumps for heating and hot water
- importing the country’s first commercial electric tractor
- implementing solar with storage batteries, and
- installing two electric frost fans.
Project summary
Company | Forest Lodge Orchard |
Industry | Horticulture |
Site region | Central Otago |
EECA funding | Technology Demonstration Fund |
Commissioned | 2020 |
With the support of EECA’s Technology Demonstration Fund, Forest Lodge imported and installed two electric frost fighting fans in 2020. Since they have been up and running, the company has saved thousands on energy bills and significantly reduced its carbon emissions. These successes have been achieved without sacrificing frost-fighting performance.
- EECA co-funding: $44,000
- Cost of frost fans: $172,000 for two (diesel equivalents $140,000)
- Annual energy savings: $8,676
- Incremental payback: 4.2 years; with EECA co-funding: 0 years
- Carbon emissions avoided per year: 11.6 tonnes
Installing the fans
Forest Lodge took a key step in its electrification journey by importing electric frost fans in 2020. These frost fans are a crucial technology for Forest Lodge, due to the prevalence of hard frosts in the region. In 2020, there were 38 frost events in Central Otago with the average frost lasting five hours. If not mitigated, these frost events can significantly reduce fruit yields.
Before Forest Lodge could install the electric fans, it had to address the limited capacity available within the local electricity network to power its transition. The company opted to upgrade its grid connection from a single-phase to a three-phase connection – at a cost of over $100,000. Three-phase connections are common in the industry and allow for greater electricity supply. This upgrade allowed Forest Lodge to also install an electric irrigation pump.
Once the electricity supply was secured, Forest Lodge purchased two 30kW, 60-amp electric frost fans from AGI Frost Fans group in South Africa, with help from EECA’s Technology Demonstration Fund. The purpose of this funding was to ‘de-risk’ the purchase for Forest Lodge and to support the early adoption of this technology in New Zealand as a demonstration.
Optimising running costs with battery power
To keep operational costs down, Forest Lodge operates one of the fans using grid electricity and the other using stored battery energy charged either by solar PV or off-peak electricity. Using this method, they also minimise the risk of the 30kW machines, which operate overnight, impacting network demand and off-peak prices.
The orchard uses a 120kWh battery array to optimise its electricity use, minimise costs and mitigate the risk of power outages.
With this approach, their average cost per kWh from the grid was only $0.11, which is significantly cheaper than a fixed price energy contract. The company sells a small amount of energy back to the grid when the spot price is high or when they have surplus solar power.
“I don’t want us to be the only zero fossil fuel farm in New Zealand. I want to use what we’ve done to really shift the needle when it comes to climate change. Our little farm down in Central Otago is saving 80 tonnes of carbon a year. If you can scale that up to 20%, 30%, 40% of horticultural operations in New Zealand, that’s a huge amount of emissions savings.”
Mike Casey, owner of Forest Lodge Orchard.
The results
Forest Lodge monitored the performance of the two new electric fans during the first frost fighting activity throughout 2023. Not only were the electric fans able to fight frost effectively, the total costs during the hours of operation were significantly cheaper.
Fighting frost with the fans required 6.6 MWh of power per year. Around half of this was drawn from the grid with the rest of the power consumption self-generated. Below is a summary of the capital and operational expenditure and emissions savings for the electric frost fans.
Costs and emissions savings |
|||
Upfront cost | Operating cost | Tonnes of CO2 emissions | |
Electric frost fans (Forest Lodge Orchard) | $171,885 | $749* | 0.3t |
Electric frost fans (100% grid) | $171,885 | $1,388 | 0.6t |
Diesel frost fans | $140,000 | $9,424** | 11.8t |
*At $0.113 per kWh. 6,609 kWh total.
**This is reached using an assumed price of diesel at $2.14 per litre, and each fossil fuel fan consuming 21 litres an hour to run.
Savings over time
Electric frost fans are the most affordable and environmentally friendly option over the fans’ lifetime.
The chart below shows the difference between the estimated total cost of the two electric frost fans used by Forest Lodge powered by a mixture of grid, solar and battery storage, over a 10-year period. This is compared to electric frost fans powered by grid electricity only, and diesel-powered frost fans.
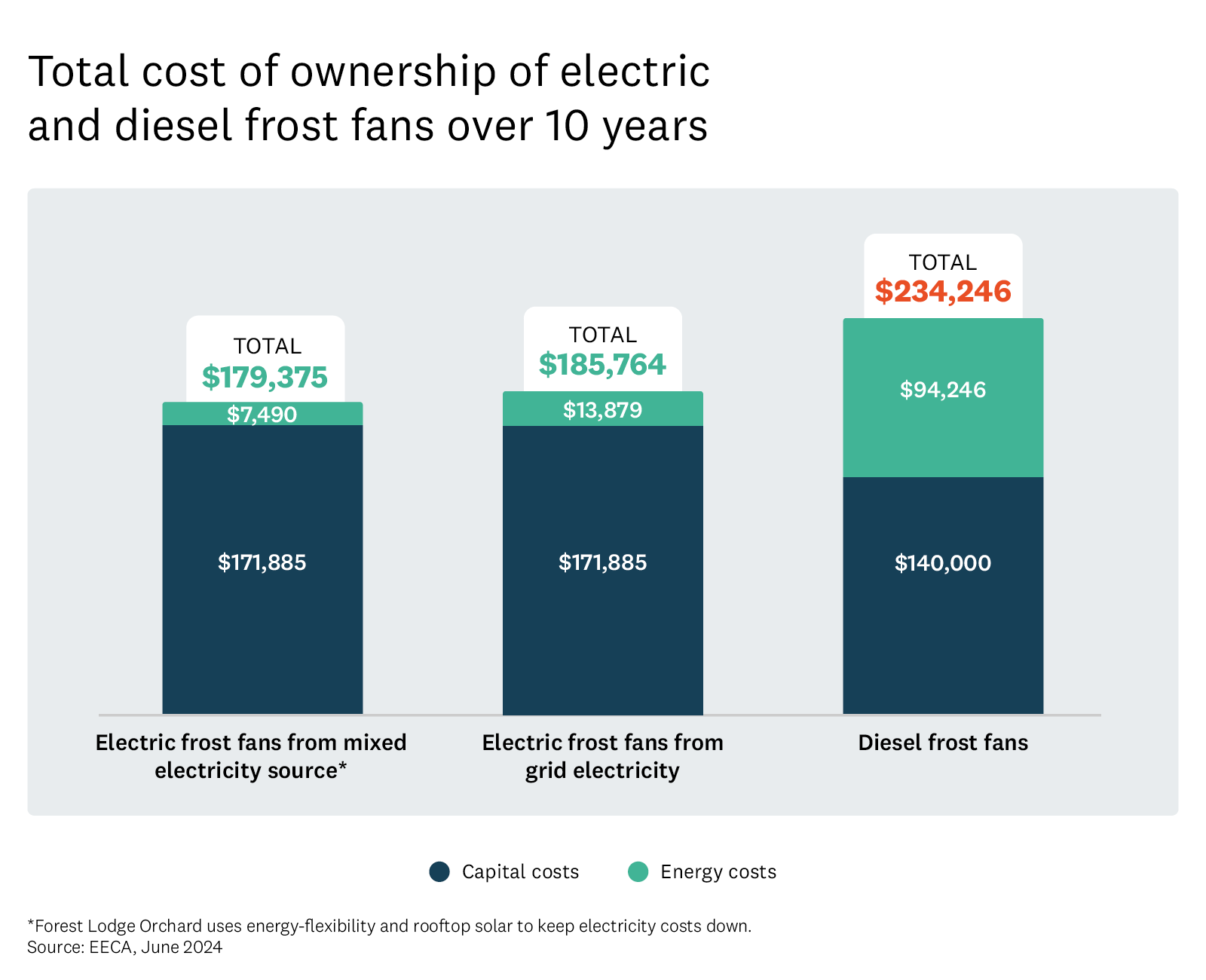
Total estimated savings of two electric frost fans over a 10-year period
Savings compared to diesel, based on Forest Lodge Orchard's experience.
- 23 % cost savings
- 98 % emissions reduction
Payback period – and the impact of solar
A 30kW electric frost fan costs around $16,000 more upfront than an equivalent diesel-powered fan, but will save around $4,000 in energy each year. At these rates, electric frost fans will pay off their additional capital expense in around 4 years.
It is important to note that Forest Lodge Orchard’s electrification is broader than just its frost fans. The orchard also has electric vehicles, an electric tractor, electric pump and other electric equipment. To help power everything the orchard spent $143,000 for solar and $129,000 for battery storage to bring its cost of electricity down and improve the farm’s energy resilience. This is in addition to the $100,000 upgrade the grid connection.
The on-site solar generation and storage lowers the cost per kW to nearly half that of grid electricity and powers much more than just the fans. This lower-priced electricity allows for a faster payback period and lower total cost of ownership than if the fans were powered solely by grid-sourced electricity.
Read next
-
Driver optional – electric tractor leads the way for low emissions rural transport
Forest Lodge Orchard drives into fossil fuel free farming.
- Case study
- Electric vehicles
- Innovation
-
Greener greens with less waste
Marlborough-based herb and salad green growers, Thymebank, have switched from coal to wood waste and nut shells for their glasshouse heating.
- Innovation
- Decarbonisation
-
McCain shares its emissions reduction journey
McCain’s Timaru site has highlighted that being innovative and trialling new technology can pay off.
- Case study
- Decarbonisation
- Renewable energy