McCain Foods has set an example to businesses looking to improve their energy efficiency, and make the switch to renewables, at its Timaru site.
The company’s experience demonstrates how reducing energy demand and adopting new technologies can lead to significant energy and cost savings.
Emissions reduction efforts pay off
As a result of making changes to how it uses energy, McCain has successfully decreased the large site’s carbon emissions by 93% (equivalent to approximately 39,000 tonnes) per year. The remaining 7% is from electricity, which has the potential to be 100% renewable in the future.
The food processing company has also been able to capitalise on the brand value of its cleaner processing, and is now planning to implement similar projects across six other sites globally.
On this page
- Business information
- The case for change
- Technologies implemented – at a glance
- McCain's journey with EECA
- Energy Transition Accelerator
- Energy graduate support
- Pulsed electric field technology
- Biomass woodchip boiler
- Mechanical vapour recompression
- The final outcome
- Key takeaways from McCain
- Resources and support
Business information
Industry: | Food processing |
---|---|
Number of employees: | 140 |
Site: | Timaru |
Total annual emissions savings: | 35,925 tCO2e |
Total annual energy savings: | 99,376 GJ |
The case for change
McCain Foods Limited is a global company that has operated for more than 60 years. It is the largest manufacturer of frozen foods – meeting almost one third of the global demand for fries. McCain NZ has two New Zealand sites – Timaru and Hastings.
The McCain Timaru site produces fries from raw potatoes, which requires several steps. Process heating and cooling is required, including for pre-heating, blanching, drying, frying and freezing the potatoes. The Timaru site is McCain’s largest New Zealand site, and prior to its journey represented 95% of McCain New Zealand’s emissions.
Approximately 9.7% of New Zealand’s greenhouse gas emissions come from process heat applications.¹ With support from EECA, McCain has undertaken extensive steps and projects to increase energy efficiency and switch to more renewable forms of energy to generate heat used in processing at its Timaru site.
In doing so, the organisation has seen a host of business benefits. In addition to the social good and clear strategic intent of the company to reduce its carbon emissions, the installation of new technologies has allowed McCain to decrease its overall operating costs.
Through these carbon cutting initiatives, McCain is also playing its part to help New Zealand transition to a low-emissions future and setting an example for other manufacturing businesses to follow.
Technologies at a glance
McCain’s clean and clever energy journey started with an Energy Assessment and an Energy Transition Pathway to map the plan to achieve their emissions reduction goals. Three new technologies were implemented as part of its overall journey.
- Pulsed electric field technology – A New Zealand first, replacing coal-generated heat for pre-cooking potatoes with an alternative technology. This project saved McCain 3,990 tCO2e and 35,595 GJ in energy savings per year.
- Mechanical vapour recompression (MVR) – Adoption of MVR for the fryer heat recovery system to improve energy efficiency and reduce fuel demand. This project has resulted in 39,943 GJ in energy savings per year.
- Biomass woodchip boiler – At the same time as adopting the MVR technology, McCain converted an existing coal boiler into a 14 MW biomass woodchip boiler. Together, these technology upgrades have saved 29,733 tCO2e per year.
“It’s important to decarbonise because our staff and our customers want to know that the food is coming from the most sustainable operations possible.”
McCain’s journey with EECA
EECA has supported McCain on its decarbonisation journey since 2016. The company was an early mover – and its work with EECA has taken a number of forms.
Energy Transition Accelerator
EECA’s Energy Transition Accelerator (ETA) programme is designed to help New Zealand’s largest businesses make technically and economically viable decisions and investments to support an energy transition pathway.
McCain’s first step was to commission an ETA assessment report, prepared by the University of Waikato. The ETA provided a high-level assessment of the business’ process heat demand, and preliminarily identified demand and supply-side options to reduce energy-related emissions over the long-term.
This fed into McCain's Energy Transition Pathway, which detailed opportunities for cleaner technology and their associated high-level estimates of capital costs and timeframes for implementation. This pathway is pictured below (with sensitive capex data and projected dates removed).
McCain opted for Option A for the fuel switching project and has now completed all the projects outlined in this plan.
Energy graduate support
EECA’s energy graduate support enables the country’s largest energy users to employ a newly trained engineer or science graduate to ensure their business commits the time and resources needed to analyse how energy is being used and the best ways to make savings.
Avinash Sampath was appointed as the Energy Graduate at McCain’s Timaru site. Over the two-year programme, he saved 1,151 tonnes of carbon emissions, and 3.66 GWh of energy – well above the target of 2 GWh. These savings are based on an energy-efficiency-first model. By reducing the site’s energy consumption, Avinash showed that there are potentially significant savings to be made through process optimisation.
“Having a staff member dedicated to addressing our energy use has been invaluable. It has given us real insight into where we can make savings, and the same data helps us build the business case for capital investments and measure success.”
Pulsed electric field technology
Pulsed electric field (PEF) processing is an efficient non-thermal food processing technique using short, high voltage pulses to treat the produce while preserving its fresh characteristics. The commissioning of the technology at McCain’s Timaru site has replaced the need for pre-cooking potatoes in vats of hot water with heat generated by burning coal.
The cutting-edge processing technology was a New Zealand-first at the time.
- Emissions savings – 3,990 tCO2e per year
- Energy savings – 35,595 GJ per year
- EECA co-funding – $250,000 for technology demonstration
- Commission date – January 2020
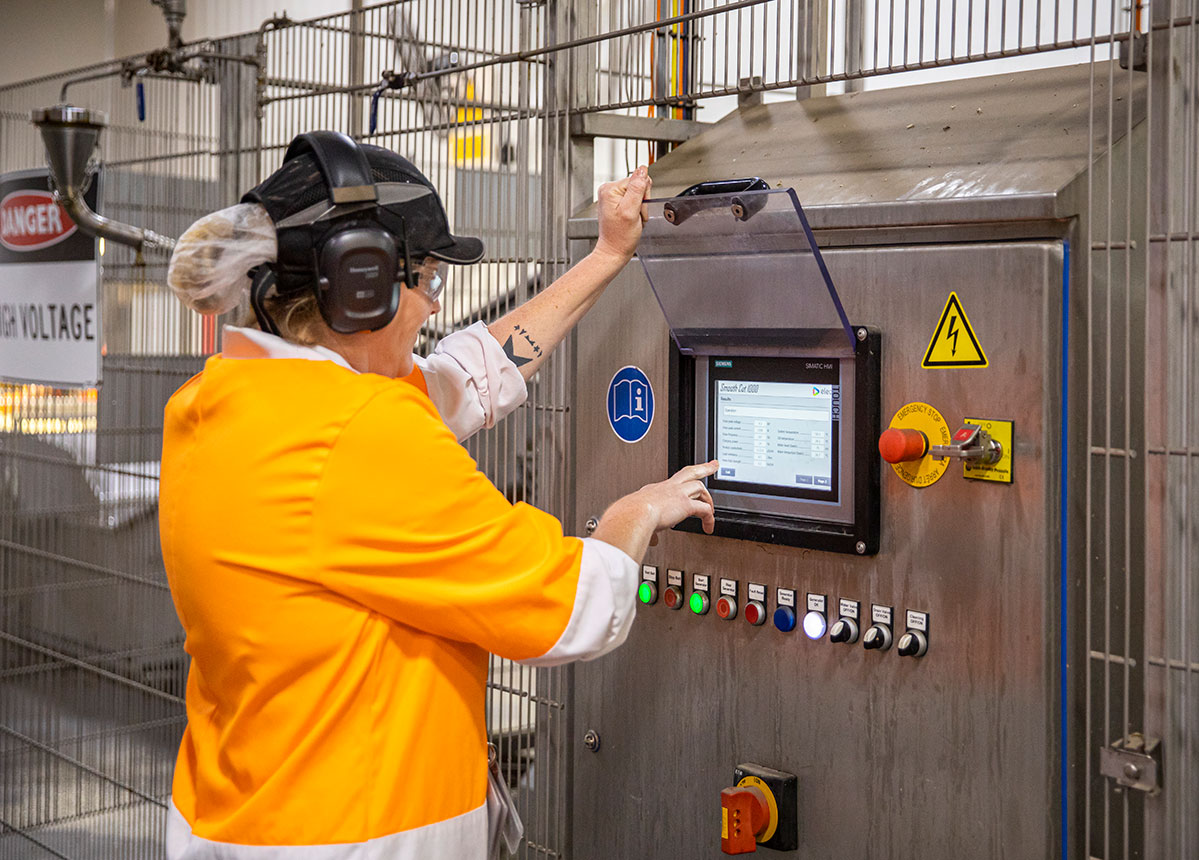
Biomass woodchip boiler
Biomass boilers are a well-known technology in New Zealand used to generate process heat. They look and operate like coal fired boilers, but are fed by biomass such as hog fuel, woodchips, sawdust or wood pellets.
McCain converted its coal boiler into a 14 MW biomass woodchip boiler to eliminate coal consumption and the associated carbon emissions.
- Emissions savings – 29,733 tCO2e per year (includes savings attributed to efficiencies created by the mechanical vapour recompression project (MVR) detailed below)
- EECA decarbonisation co-funding – $2,876,500 (combined with the MVR project)
- Commission date – July 2022
McCain’s biomass boiler project included the construction of a purpose-built storage facility for the wood chip. The storage facility allows the chip to stay dry to achieve maximum fuel efficiency. When fuel is needed it is transported by conveyer belt to the boiler room.
The conversion of the boiler completely removed the need for coal on-site and has improved local air quality.
Wood has a much lower ash content than coal, and the ash that is produced is less toxic. The reduced ash volumes have eased ash handling and stormwater quality has improved with reduced ash contamination. The remaining ash will be used for wider sustainable practices such as composting.
Biomass can offer substantial operational cost savings as the NZ ETS price increases
The chart below highlights the savings biomass can achieve compared to coal as the NZ ETS price increase. When the NZ ETS price reaches $90 t/CO2 biomass will a cheaper option, which will become increasingly cheaper over time at the NZ ETS prices continues to rise. These operational savings can compound over time, offering businesses substantial savings over a biomass boiler’s lifetime.
Mechanical vapour recompression
Mechanical vapour recompression (MVR) systems recover and reuse energy normally lost through evaporation. Because of the ability to use and upgrade wasted energy, MVR can significantly increase the efficiency of industrial heating and evaporation processes. They achieve this by recompressing vapour for reuse as a heat source for the same process from which the heat was recovered.
McCain installed an MVR system for the fryer heat recovery system, to improve energy efficiency by lowering steam demand and therefore reducing biomass use. This was the first project of its kind in New Zealand and has been hugely successful.
Overview
- Energy savings – 39,943 GJ per year (approx.)
- EECA decarbonisation co-funding – ($2,876,500 for both the MVR project and the boiler conversion)
- Commission date – November 2022
The MVR system has not only helped McCain reduce energy demand, and subsequent cost and emissions, but has also resulted in other benefits and process improvements for the site.
Reducing direct injection of steam into hot utilities has helped the plant reduce boiler feedwater usage by 17,600 m3/year, which in turn has reduced the chemical used for treating the feed water.
The installation of a condenser and removal of an existing scrubber attached to the fryer exhaust stack has led to improved collection of saturated oil in the oil separator.
Spraying heated boiler feedwater into the factory condensate return tank has helped sub-cool the tank condensate temperature, reducing the amount of flashed steam losses.
The final outcome
Prior to beginning its decarbonising journey, McCain’s Timaru site produced 38,852 tonnes of process heat carbon emissions on-site. The site has now completed its clean and clever journey, successfully reducing almost all of its process heat emissions, except for a small amount from biomass use, and those generated through electricity use (which has the potential to be 100% renewable).
McCain has benefitted from significant energy cost reductions, reduced product waste, water savings (of almost 50%), improved air and stormwater quality and reduced ash.
Undertaking these projects has also put McCain in a position to make substantiated sustainability claims in its advertising, particularly after winning a New Zealand Sustainability Award 2022, for this work.
By taking action early, McCain is staying ahead of climate mitigation regulation, and building its brand as a leader in sustainable food production.
Explore how other businesses are benefiting from reducing emissions
Key takeaways from McCain
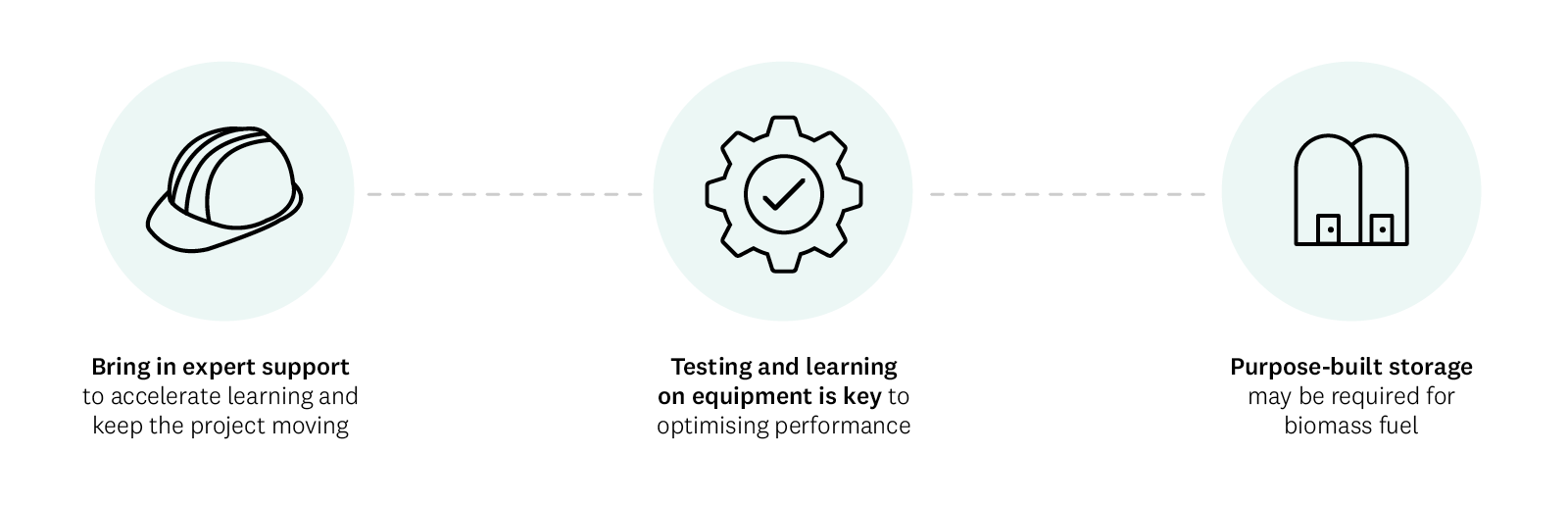
Lessons to share
It is normal for businesses to face barriers along their energy efficiency and fuel switching journey. McCain has identified and learned a range of lessons that can be applied to other business looking to follow a similar process.
- Bring in expert support
An external consultant helped McCain overcome initial issues with the Mechanical Vapour Recompression system that had led to some delays with commissioning.
The commissioning time to operationalise the new Mechanical Vapour Recompression system took longer than anticipated. This was largely due to uncertainty surrounding the new technology which had never been implemented in this process in New Zealand before, as well as supply chain delays with a critical part of the system. McCain was able to overcome this by employing an energy consultant who worked closely with the project team to systematically overcome the issues.
Although the commissioning took longer than expected, the system has since been a huge success, saving almost 40,000 GJ of energy per year. This highlights that the risk that McCain took adopting the new low-emissions technology paid off, and it has huge potential for other businesses looking to significantly reduce energy demand and medium-long term costs.
- Expect to test and learn
The McCain team had to problem-solve some initial operating issues with the biomass boiler to get it working as expected.
Initially, the converted biomass boiler was experiencing incomplete combustion of woodchip and there were creeping temperatures of the burning woodchip fuel near the feeders. This was resulting in the boilers shutting down and fire sprinklers activating as the temperatures were reaching their maximum safety point.
The team quickly worked to understand and overcome the underlying issue. In response, the speed of the fuel feeding fan and the gap in-between the air flow dampers were increased. Since then, the woodchip boiler has been operating as expected and the team are happy with the project’s overall success.
- Consider biomass storage
McCain overcame potential issues around biomass storage by building a purpose-built storage unit. Businesses looking to switch to biomass fuel need to consider storage and handling before they commission new technology.
When determining the size and design of their storage facility, McCain considered fuel delivery schedules (taking into account possibly supply chain disruptions), the boiler operating load and the moisture content. It also designed it to minimise health and safety hazards.
“We’ve taken the lessons that we’ve learned from this pathway and we’re rolling it out globally, to six other sites.”
Resources and support
Many businesses want to decarbonise, but don’t know where to begin or what steps to take.
Large energy-using businesses can take a similar path to McCain and start with an energy audit or apply for the EECA Energy Transition Accelerator programme.
References
¹ 2022 data from EECA’s Energy End Use Database and the Ministry for the Environment's Greenhouse Gas Inventory(external link)
Further reading
-
The business good of decarbonisation
By playing your part in New Zealand’s transition to a low emissions future, your business can reap financial and non-financial benefits.
-
Clean alternatives to fossil fuelled heat plants
An overview of low-emissions technologies for industrial process heat.
-
International Technology Scan - Alternative Technologies for Process Heat
This report provides an inventory of a wide range of internationally available technologies that could be applied to New Zealand industry for energy efficiency and/or reducing emissions.